案例一:某公司硝化项目,2500吨/a通量。
案例分析价值:关键词有,硝化反应、快速反应、常温进料、低温反应和强放热;项目难点是,物料有高浓混酸,不能做预冷,只能常温进料,且为强放热反应,反应前段需要压低温度,反应后段要保持-11℃到-5℃低温,分区控温是难点之一;物料流量、线速度、阻力、混合能力和反应时间,相互影响,要找到合适的平衡点,要求设备的设计考虑到工艺调节的能力;客户对系统的自动控制能力亦提出了要求。
釜式化工过程描述:开启冷冻盐水降温,放入硫酸X公斤,再开启搅拌放入发烟酸Y公斤,搅拌10分钟取样;当温度低于30℃以下时,缓慢加入硝酸Z公斤;当温度低于-7℃时,即可慢慢加入原料,整个加料过程温度不能超过-5℃,以温度为准,约2小时左右;投料完毕反应30分钟打料稀释;稀释锅内提前放入适量清水,开启冷冻盐水,降温至10℃以下,把反应好的硝化料缓慢打入稀释锅内,温度控制在10℃左右;打料完毕保温30分钟左右打进压滤机,水洗至PH5-7;吹干卸料进烘房。
微化工工艺过程设计:
不同于传统釜式化工,微化工更强调化工装备和工艺的匹配度,那央微化采用微化工连续流工艺设计该项目,也即“微化工三段式工艺逻辑”,微分散预混过程、微反应强化过程和延时熟化三个阶段,同时针对不同阶段的放热强度,设计不同温区的控制策略。

图1:硝化项目微化工工艺过程设计
微化工核心参数匹配:
不论是釜式化工还是微化工都遵循化工的本质,也即“三传一反”:传质传动传热和反应动力学,我们基于“三传一反”这一理论依据和“微化工三段式工艺逻辑”,来设计和匹配微化工装备的核心参数。
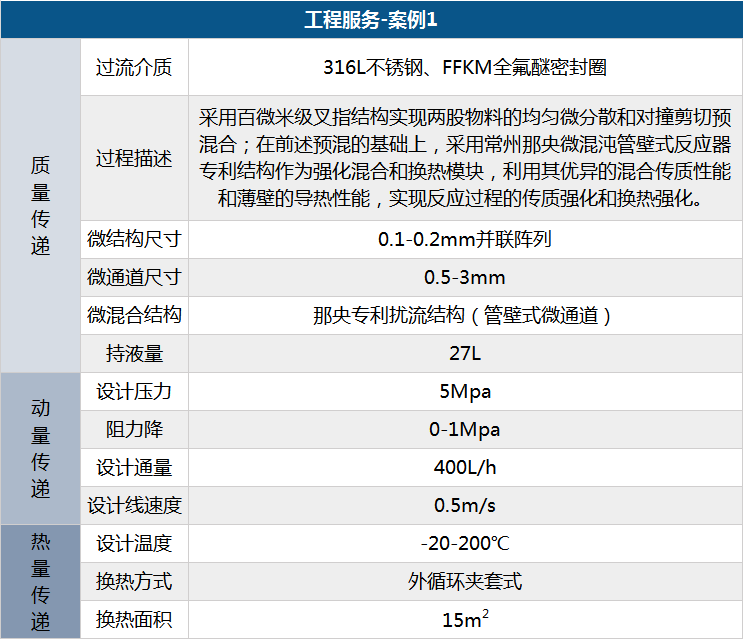
案例二:某公司自由基均聚反应,3000吨/a通量。
案例分析价值:关键词有,自由基引发、开环聚合、快速反应、高温、高压和强放热;项目难点是,工艺条件是反应温度170℃到200℃,压力2Mpa,反应时间1-10min,温度控制不好的话,原料会瞬间分解,剧烈放热,进而引发链式反应,产生大量气体和引起高压,增加系统危险性。
釜式化工过程描述:一共三股物料,将两股互溶物料混合好后置于2吨反应釜中,滴加另一物料,控制反应温度180℃,微负压排出反应产生的小分子气体,整个反应过程持续3天。
微化工工艺过程设计:
不同于传统釜式化工,微化工更强调化工装备和工艺的匹配度,那央微化采用微化工连续流工艺设计该项目,也即“微化工三段式工艺逻辑”,微分散预混过程、微反应强化过程和延时熟化三个阶段,同时针对不同阶段的放热强度,设计不同温区的控制策略;针对产物中的低沸点小分子气体,采用闪蒸粗分方法初步分离,粗分液和母液交给用户现有分离系统处理。
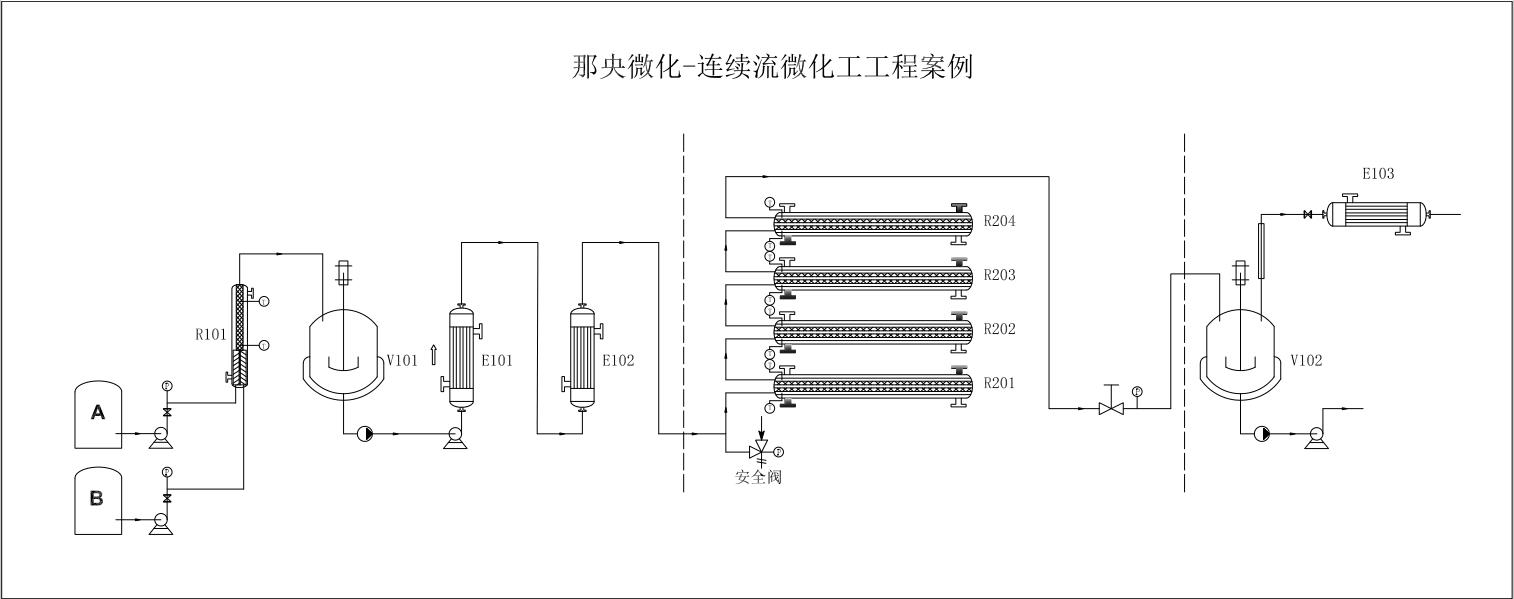
图2:自由基均聚项目微化工工艺过程设计
微化工核心参数匹配:
不论是釜式化工还是微化工都遵循化工的本质,也即“三传一反”:传质传动传热和反应动力学,我们基于“三传一反”这一理论依据和“微化工三段式工艺逻辑”,来设计和匹配微化工装备的核心参数。

案例三:某公司高温盐酸参与的反应,500吨/a通量。
案例分析价值:关键词有,浓盐酸、高温、高压、耐腐蚀、强放热;项目难点一,原料之一为盐酸,客户zhi定微通道反应器采用碳化硅材质来实现,高压2Mpa,要求工业生产的稳定性;难点二是,反应温度高达160℃,放热强度大,前段要求加大降温力度,后段要求保温,维持反应温度160℃,需要多段控温;难点三是,反应过程产生气体,需要在连续反应的过程实现气体的连续排放。
釜式化工过程描述:一股物料置于釜内,预冷到10℃,滴加另一股物料,控制反应温度不超过160℃,滴加完成,保温160℃直至最终完成反应。
微化工工艺过程设计:
不同于传统釜式化工,微化工更强调化工装备和工艺的匹配度,那央微化采用微化工连续流工艺设计该项目,也即“微化工三段式工艺逻辑”,微分散预混过程、微反应强化过程和延时熟化三个阶段,同时针对不同阶段的放热强度,设计不同温区的控制策略。
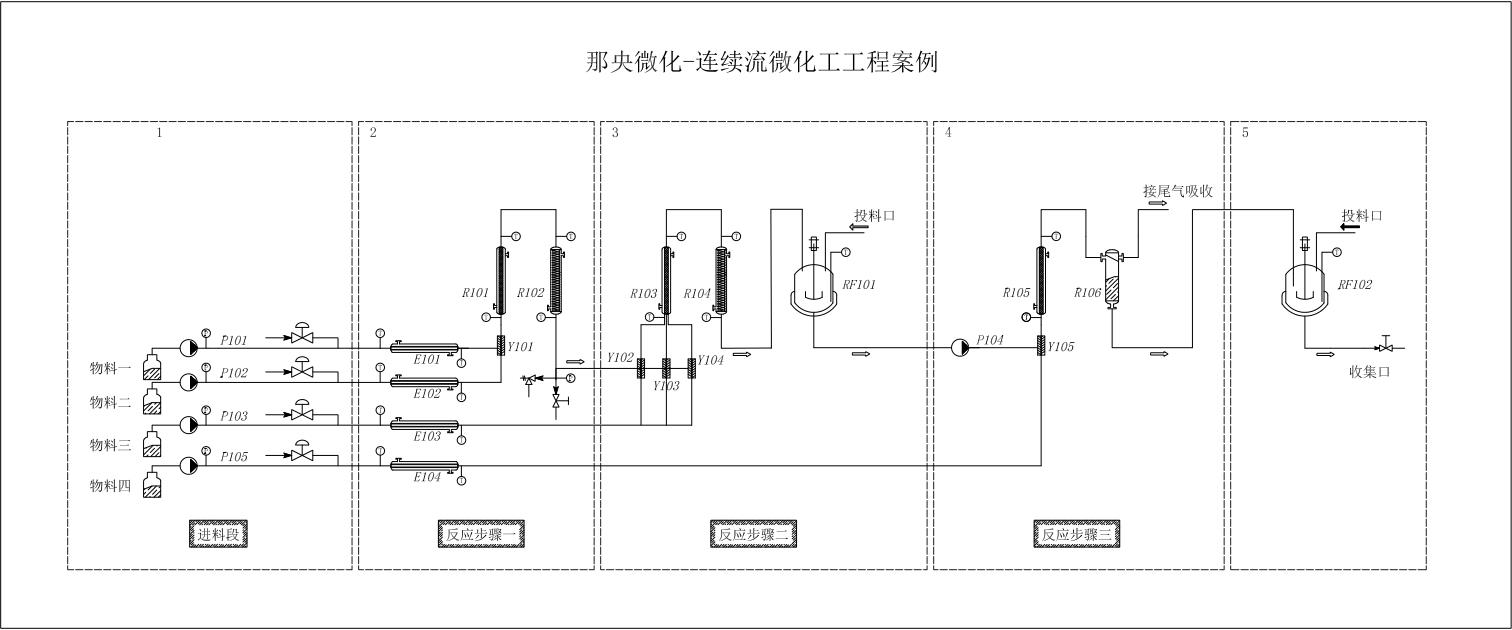
图3:盐酸项目微化工工艺过程设计
微化工核心参数匹配:
不论是釜式化工还是微化工都遵循化工的本质,也即“三传一反”:传质传动传热和反应动力学,我们基于“三传一反”这一理论依据和“微化工三段式工艺逻辑”,来设计和匹配微化工装备的核心参数。
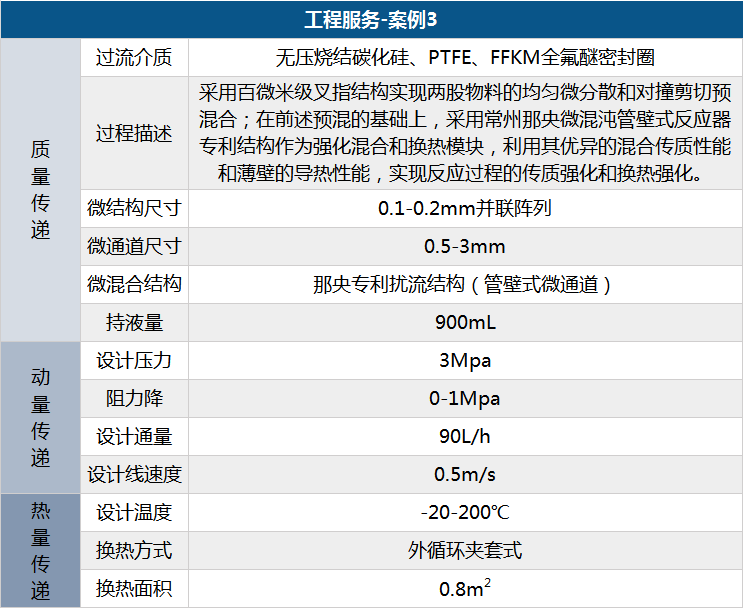
案例四:某公司氧化反应,500吨/a通量。
案例分析价值:关键词有,高温、高压、耐腐蚀、气液反应;项目难点一,原料之一为有腐蚀性,以及鉴于高温(180℃)和高压(2Mpa)的要求,采用钛材TA1来制造该项目微化工装备;难点二是,要精确控制反应时间,过反应会导致原料过氧化,产生副产杂质。本项目微化工装备的设计难点在于气液混合反应过程不能采用常规的微通道混合结构,因为常规的微通道混合结构中,液体相对气液粘度更大、流速更慢、且有拖尾现象,会导致管道中反应的不均一。
釜式化工过程描述:传统釜式工艺通过鼓气到搅拌釜底部的方式完成反应,通过控制反应时间来抑制副产物的转化率,其缺点是难以实现更高的温度和压力,增加母液分离步骤,增加工序和成本。
微化工工艺过程设计:
不同于传统釜式化工,微化工更强调化工装备和工艺的匹配度,那央微化采用微化工连续流工艺设计该项目,也即“微化工三段式工艺逻辑”,微分散预混过程、微反应强化过程和延时熟化三个阶段,同时针对不同阶段的放热强度,设计不同温区的控制策略,同时针对气液平推流的要求优化了微通道结构,增加气液分离模块实现气液分离和连续流反应的耦合。
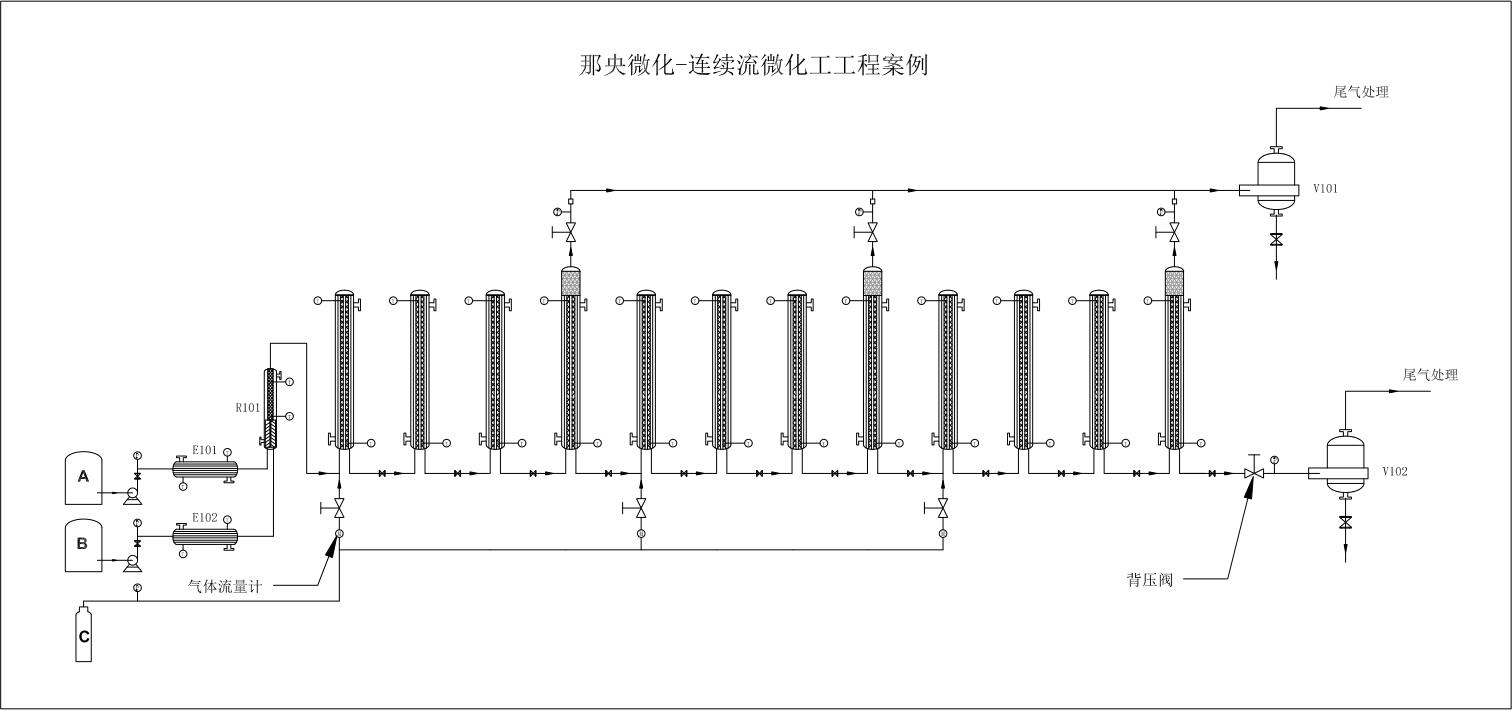
图4:氧化项目微化工工艺过程设计
微化工核心参数匹配:
不论是釜式化工还是微化工都遵循化工的本质,也即“三传一反”:传质传动传热和反应动力学,我们基于“三传一反”这一理论依据和“微化工三段式工艺逻辑”,来设计和匹配微化工装备的核心参数。
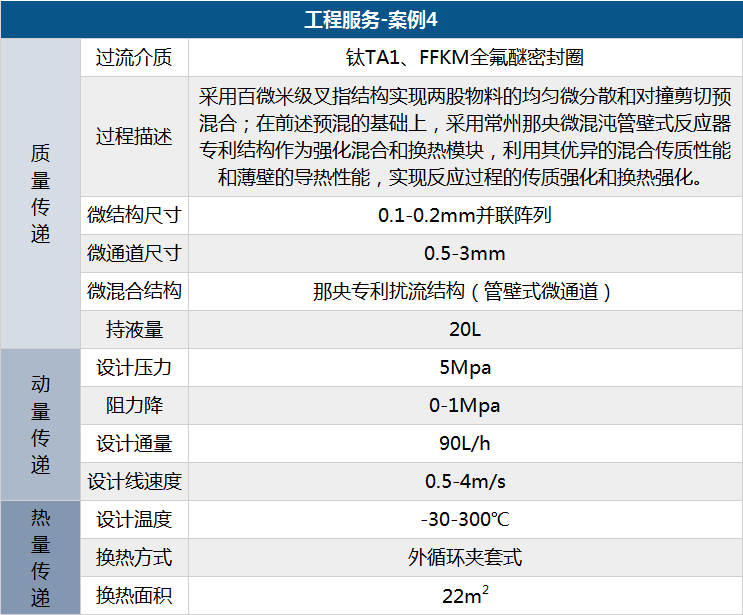
案例五:某公司产固反应,1000吨/a通量。
案例分析价值:关键词有,无机反应、快速反应、固体产物、确保连续流反应时间;项目难点一,反应产物为固体,固含量达到40%,极易造成通道堵塞;难点二是,需要确保连续流反应时间不低于30s,时间太短产物晶体未成形,时间太长,反应通道堵塞风险增加。
釜式化工过程描述:两股物料同时加入反应釜中,搅拌并控制反应时间,缺点在于两股物料混合不均一,导致产物晶体粒径不均一,产品质量难以保证。
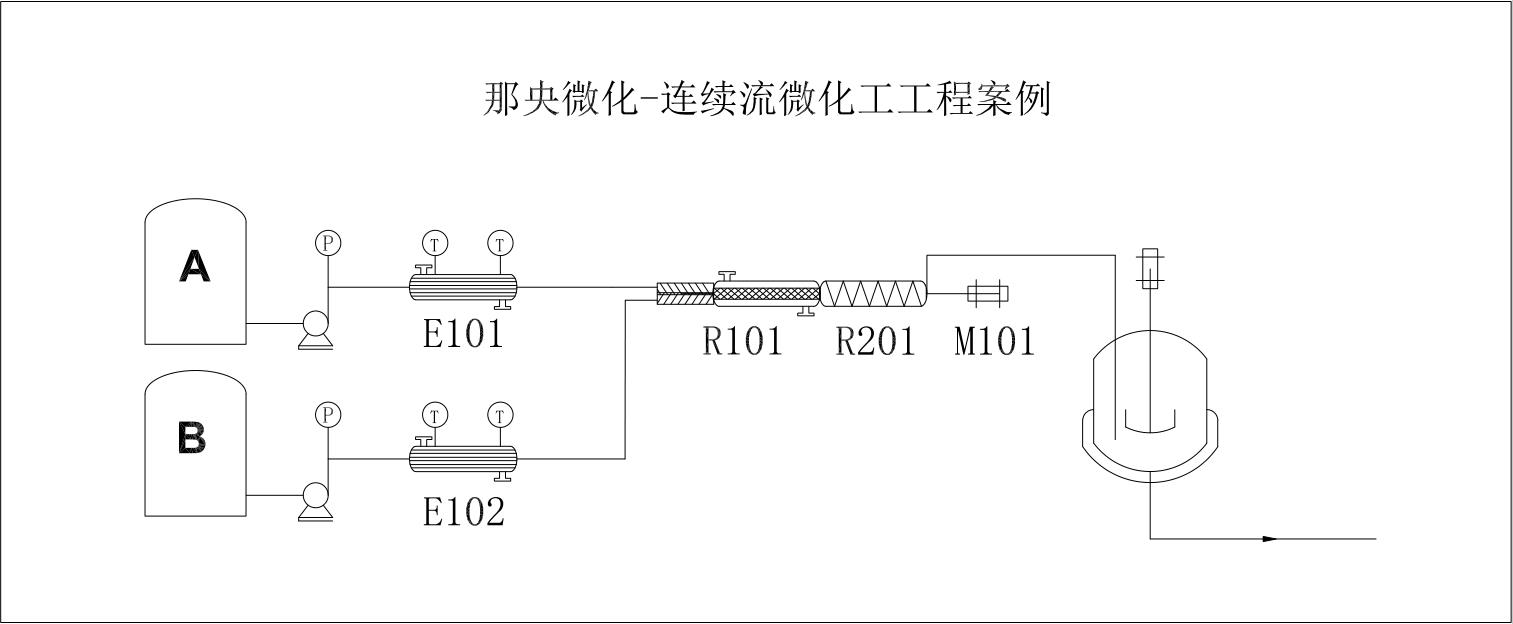
图5:产固项目微化工工艺过程设计
微化工工艺过程设计:
不同于传统釜式化工,微化工更强调化工装备和工艺的匹配度,那央微化采用微化工连续流工艺设计该项目,也即“微化工三段式工艺逻辑”,微分散预混过程、微反应强化过程和延时熟化三个阶段,同时针对不同阶段的放热强度,设计不同温区的控制策略。本项目首先要利用微分散模块,实现两股物料按照设定比例均匀混合,其次是利用连续流微通道平推流的特点实现反应时间的精确控制。
微化工核心参数匹配:
不论是釜式化工还是微化工都遵循化工的本质,也即“三传一反”:传质传动传热和反应动力学,我们基于“三传一反”这一理论依据和“微化工三段式工艺逻辑”,来设计和匹配微化工装备的核心参数。

案例六:某公司加氢反应(简略)。
案例分析价值:固定床负载固体催化剂,高温高压反应,产生反应气体,该项目是连续流加氢反应的典型代表。
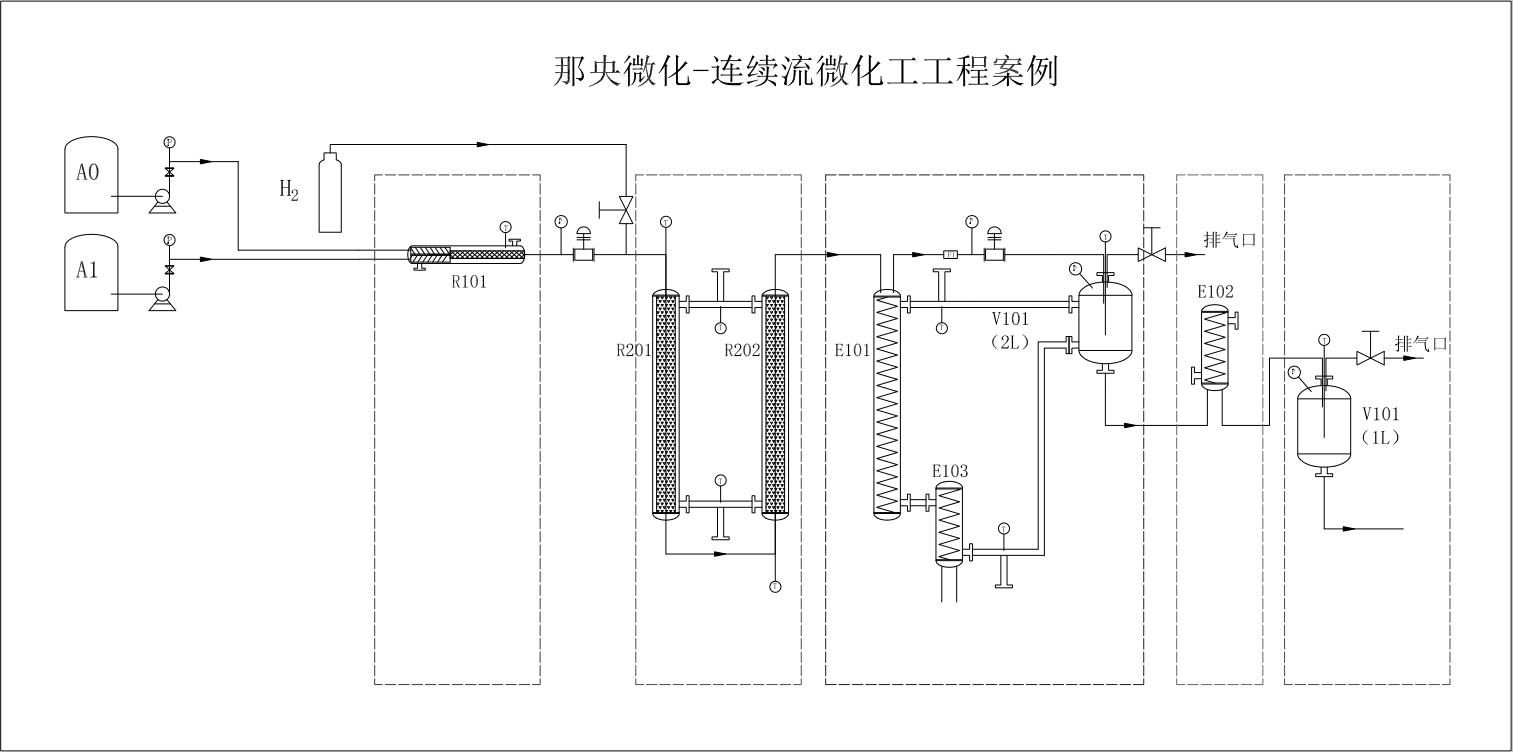
图6:加氢项目微化工工艺过程设计
案例七:某公司强腐蚀反应(简略)。
案例分析价值:该项目采用四氟管式反应器加扰流内构件制造,满足项目耐腐蚀、高温(180℃)、高压(1.5Mpa)的要求,虽然四氟管式反应器换热能力较差,但本项目并非强放热反应。该项目是连续流微化工工艺、微化工设备和成本控制匹配性非常好的一个典型代表。
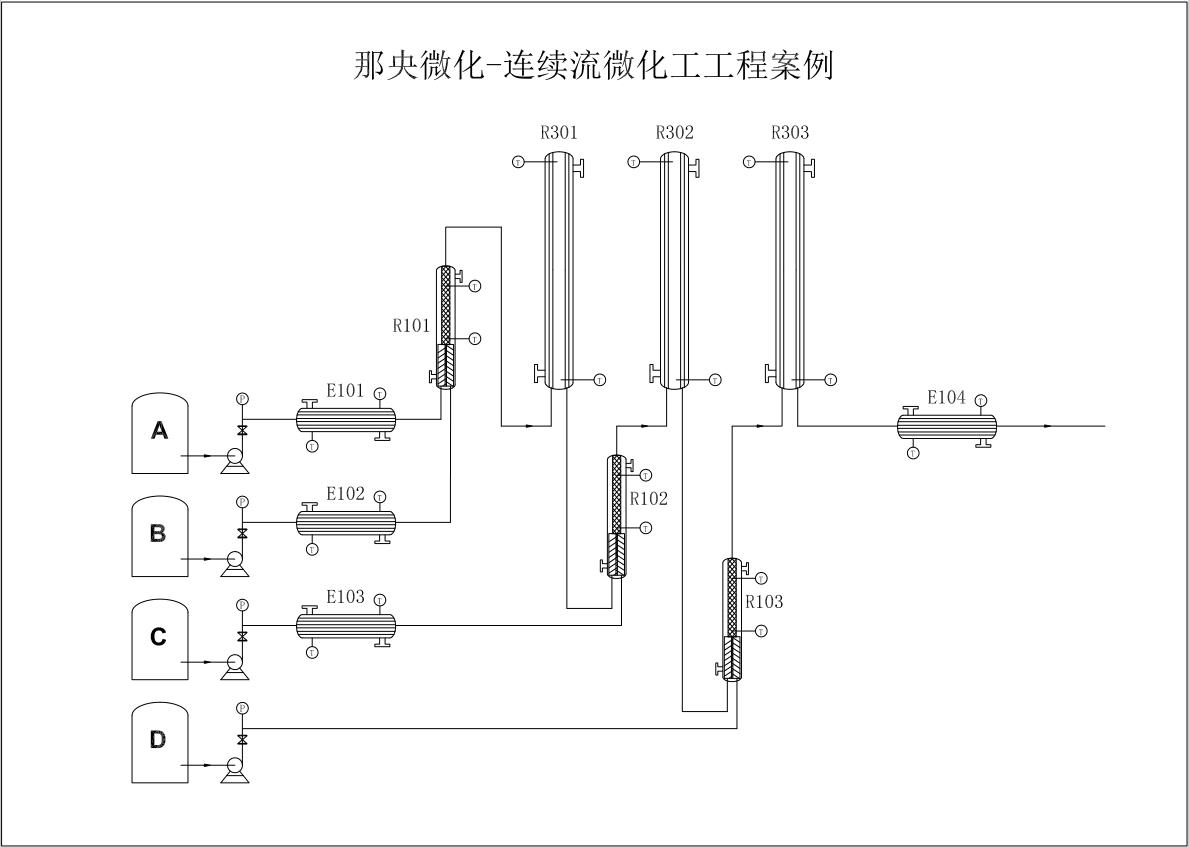
图7:强腐蚀项目微化工工艺过程设计