连续流微反应器作为化工合成领域的杰出性技术,通过毫米级通道内的精准控制,实现了传统釜式反应难以企及的效率与安全性。其核心原理与操作模式,正在重塑精细化工、药物合成及新材料开发的生产范式。
一、微观通道中的反应机制
1.强化传质与传热:微通道的直径通常为50-1000微米,比表面积可达传统反应釜的100倍以上。在硝化反应中,某企业通过微反应器将硝酸与甲苯的混合时间从釜式反应的30分钟缩短至3秒,传质效率提升98%,副产物二硝基甲苯生成量降低至0.5%以下。
2.精准停留时间控制:通过调节泵速(0.1-100 mL/min)与通道长度(0.5-10米),可精确控制反应物在通道内的停留时间(秒级至分钟级)。某药企在格氏试剂制备中,将反应时间从釜式的2小时压缩至45秒,收率从72%提升至91%。
3.即时热移除能力:夹套式微反应器可实现10000 W/m2·K的换热效率,是传统釜式反应的1000倍。在强放热反应(如氧化反应)中,某新材料公司通过微反应器将温度波动控制在±1℃以内,避免热失控风险。
二、操作模式与工艺优势
1.连续进料与产物分离:采用计量泵将反应物按化学计量比连续注入通道,产物经在线分离模块(如膜分离、萃取)直接收集。某香料企业通过微反应器实现连续化生产,产能从釜式的50 kg/天提升至2吨/天。
2.多步串联反应:通过模块化拼接通道,可完成“一锅法”多步反应。某API合成中,将磺化、还原、成盐三步反应集成于微反应器,总反应时间从72小时缩短至8小时,E因子(废弃物/产物质量比)降低60%。
3.本质安全设计:微通道内反应物存量仅毫升级,远低于釜式反应的百升级,可有效控制风险。某高校实验室在光催化重氮化反应中,通过微反应器使用易爆的重氮盐,事故率降为零。
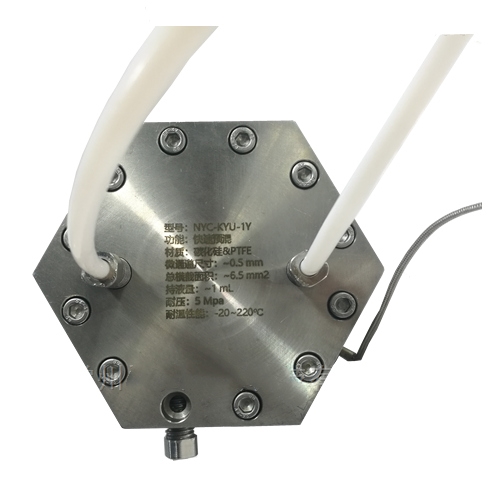
三、技术挑战与未来方向
当前微反应器仍面临通道堵塞(如高粘度体系)、催化剂固定化(如均相催化)等挑战。未来,3D打印微通道、光催化-微反应耦合、AI过程强化等技术将推动其向更复杂反应体系渗透。某研究团队已开发出光响应微通道,通过光照调控通道表面润湿性,实现反应选择性动态调节。
连续流微反应器不仅是工艺优化工具,更是绿色化学的践行者。其“小通道、大能量”的特性,正在推动化工行业从“间歇式生产”向“连续化制造”转型,为碳中和目标提供技术支撑。